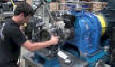 |
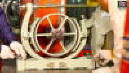 |
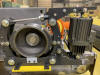 |
|
Brake
failure and cause: |
1. The brake wheel cannot be stopped (weight slides down)
Cause of
failure: |
-
The hinge of the
lever is stuck.
-
The brake wheel
and friction plate have oil on them.
-
Solenoid core
does not have enough travel.
-
Severe wear on
brake wheel or friction plate.
-
Loose and
damaged mainspring.
-
Lose lock nut,
loose tie rod.
-
The hydraulic
push brake impeller does not rotate properly.
|
Remedy: |
-
Clear the jam
fault
-
Oil Cleaning
-
Adjusting the
Brake
-
Replacing
Friction Blades
-
Replacing
Friction Blades
-
Tighten the lock
nut.
-
Overhaul of
propulsion mechanism and electrical parts
|
2. Brake does not
release Cause of failure. |
-
Burned out
solenoid coil
-
Disconnect the
wire to the solenoid
-
The friction pad
sticks to the brake wheel.
-
The movable
hinge is stuck
-
Excessive force
in the mainspring or too much counterweight
-
Bend the brake
top lever, does not push the electromagnet (on the hydraulic
push rod brake)
-
Improper use of
fluids
-
Impeller jamming
-
Voltage is less
than 85% of rated voltage, electromagnet suction force is
insufficient
|
Exclusion Method: |
-
Replacement
-
Connect the
wires
-
Cleaning with
kerosene
-
Eliminate
jamming, lubrication
-
Adjusting the
mainspring force
-
Top bar
straightening or replacing the top bar.
-
Changing the
fluid according to the working environment temperature
-
Adjusting the
actuator mechanism and checking the electrical parts
-
Identify and
troubleshoot the causes of voltage drop
|
3. The brake is hot,
the friction plate smells burnt and wears out quickly. Cause of
failure. |
-
The brake shoes
are not evenly and completely disengaged from the brake
wheel after the brake is released, resulting in friction.
-
The gap between
the two brake shoes and the brake wheel is uneven or too
small.
-
Short-stroke
brake auxiliary spring is damaged or bent.
-
The working
surface of the brake wheel is rough.
|
Elimination method: |
|
4. The brake easily
leaves the adjustment position, and the braking torque is not
stable enough. Cause of failure |
|
Exclusion Method: |
-
Tighten the nut
-
Replacement
|
5. Electromagnet is
hot or loud. Cause of failure. |
-
Excessive
mainspring force
-
The lever system
is jammed
-
The armature and
the core are not correctly positioned.
|
Exclusion Method: |
|