Suction pipe |
|
- Place the
pump or pump unit as close as possible to the pumped liquid.
- The pipe
must be as short as possible.
Run the pipe so it slopes upwards
- toward the
pump to prevent the formation of air pockets.
|
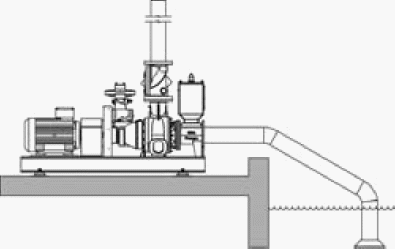 |
|
|
- If the pipe
tapers, the pipe must slope downwards toward the pump. Place
a shut-off valve between the float chamber and MP to prevent
overpressure on the MP.
|
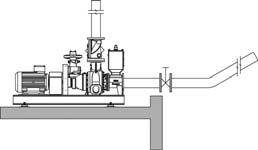
|
|
|
- Lay the pipe
so as to prevent the formation of air pockets.
- Use the
least possible number of bends.
- Bends must
have the largest possible radius.
- The pipe
system must be completely airtight.
- In the case
of a non-self-priming pump, in which the liquid does not
flow towards the pump, install a foot valve with a
sufficiently large flow capacity.
|
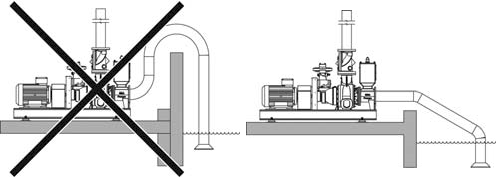 |
- In the case
of polluted liquids, always install a suction strainer or
solids separation screen with a sufficiently large net
opening area. The filtration particle size of the suction
strainer must be equal to or less than the solids handling
specification of the pump.
|
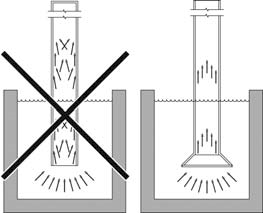
|
|
|
- When there
is a change of diameter in the piping, use an eccentric
reducer to prevent the accumulation of air.
|
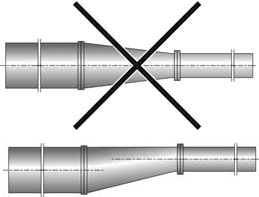
|
|
|
- Make sure
that the liquid intake will remain sufficiently submerged
beneath the liquid surface so no air will be drawn in even
when the liquid is at its lowest level.
|
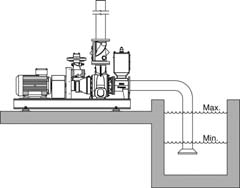
|
|
|
- Make sure
the length of the pipe between a bend and the pump is at
least four times the diameter of the pipe, especially when
there is little margin between the available and required
NPSH. A bend prevents the smooth inflow of liquid to the
pump impeller and can have a negative impact on the suction
conditions.
|
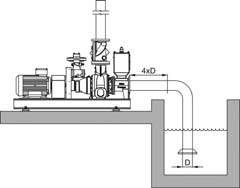
|
|
|
- When a
T-junction is installed, use one with an inflow bend.
|
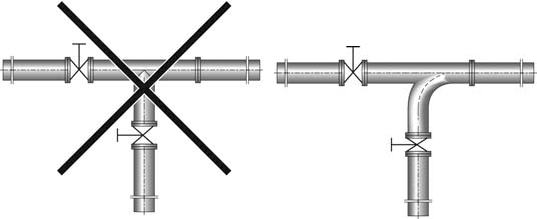 |
|
In the case of self-priming pumps fitted with a separate suction
bend, this bend must never be removed or rotated. |
- For liquids
with a low viscosity, either install a foot valve with a
diameter equal to or greater than that of the suction valve
or install the piping without a foot valve in a
U-configuration (see technical specifications BA series).
- Do not
install a foot valve when pumping high viscosity liquids.
The foot valve causes extra pipe losses.
- To eliminate
any air or gases present in the pump or suction pipe, the
pressure pipe can be fitted with a bypass line. The use of a
bypass line will eliminate air from the pump more quickly.
See also ‘Pressure pipe’.
- In some
situations the temperature of the liquid may be so high that
the pump requires pre-pressure relative to the NPSH in the
line (see technical specifications BA series).
|
Pressure pipe |
- The designer
of the installation is responsible for including the
safeguards, such as protection against overpressure.
- To prevent
pipe losses, use the fewest number of bends possible.
- When the
pressure pipe is long or when a non-return valve is used in
the pressure pipe directly after the pump, install a bypass
line, fitted with a shut-off valve. Connect the bypass line
to the suction line or suction point.
- To bleed air
from the pump more quickly, the bypass line must be
connected to the supply tank or suction point.
|
WARNING
Prevent sudden closure of the pressure pipe that would cause
water hammer. |
- If there is
a danger of water hammer, install a bypass, accumulator or
pressure safety valve in the pressure pipe.
|
Suction strainer
When pumping polluted liquid or liquid that may contain solid
particles, install a suction strainer in the suction opening. |
- When
selecting the suction strainer, carefully consider the mesh
width so pipe losses are kept to a minimum. The net opening
area of the suction strainer must be at least three times
the crosssectional area of the suction pipe.
- In the case
of polluted liquids, always install a suction strainer with
a sufficiently large net opening area. The filtration
particle size of the suction strainer must be equal to or
less than the solids handling specification of the pump.
- Install the
suction strainer such that maintenance and cleaning are
possible.
- Make sure
the liquid being drawn in has the expected viscosity and can
easily flow through the suction strainer. Heat the suction
strainer if necessary.
- Consult the
technical specifications for the BA series for the maximum
allowable particle size (solids handling capacity).
|