Thread
cutting procedure
- Clamp the part in the lathe using
a live centre if necessary.
- Turn the OD to the target major
diameter and include a chamfer on the end at least 0.5
mm smaller than the minor diameter of the thread profile
to be cut.
- If permissible, cut a thread
relief using a grooving tool (as shown in Figure 1
and the two video thumbnail images above). The thread
relief should be slightly less than the minor thread
diameter.
- Adjust the gearbox levers on the
front of the headstock to cut the proper thread pitch.
- Set the threading tool so it is
aligned parallel to the X-axis Figure 2
- Touch off on the part and zero
the X-axis.
- Cut a light (.03-.05 mm) scratch
pass across the surface of the part to be checked with a
thread gage for accuracy.
- If the pitch of the scratch pass
measures correctly, begin cutting the thread to depth;
start with deeper depths of cut (.25 mm in aluminium,
0.15 mm in steel) and make progressively shallower cuts
as the thread gets deeper and the threading tool begins
to leave a worse finish)
- As you approach final thread
size, use a fine file to carefully debur the rough edges
of the major diameter (unless using a full profile
insert, which deburrs the major diameters automatically,
as discussed above).
The procedure for making
an actual cut is:
- Check the direction of the
threading direction by engaging the half-nut with the
tool a safe distance from the part; for this example, we
will thread toward the chuck
- Adjust the spindle speed to a low
setting (100-300 rpm) depending on how brave you are
- Position the tool in a safe
starting location to begin cutting the thread
- Advance the tool toward the part
the distance (depth of cut) you wish to cut
- Engage the half-nut for threading
(it’s safest to leave this engaged for the duration of
the threading session)
- Turn the spindle ON in the FWD
direction and allow the tool to make a cut
- Turn the spindle OFF before the
tool reaches a shoulder (if not exists); you can use the
foot brake to stop it quickly if needed; if you stop too
early, simply bump the power switch to continue the cut
or rotate the chuck by hand
- Retract the tool a safe distance
from the part in the X-direction
- Turn the spindle ON in the REV
direction to allow the tool to return to a safe starting
location
- Repeat steps until the desired
minor or pitch diameter is reached.
Note: The thread dial indicator (Figure
3) can be used for engaging the half-nut at the correct
moment. This is to be used if the reverse method is
not used.
|
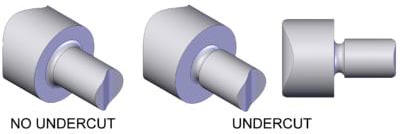
Figure 1
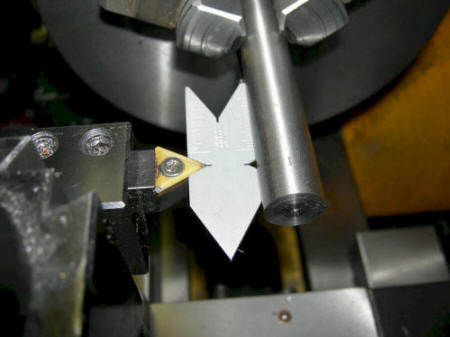
Figure 2
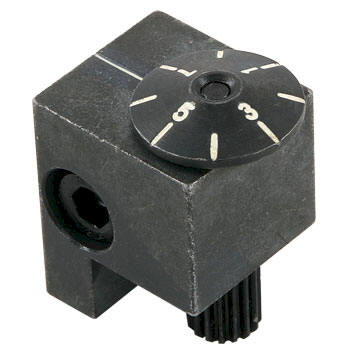
Figure 3 |