Clamping methods |
Clamping device are used to minimize the
distortion during the machining process. Once the workpiece
is located, it is necessary to hold it against the machining
force. The mechanism used for this is known clamps. They are
work holding devices usually positioned above the supporting
surfaces. |
Videos |
Factors to consider when calming work:
|
- Shape of workpiece
- Type of material of workpiece
- The rigidity of workpiece
- Pressure excreted by drill or cutting
tool
- Ease of locating and c lamping
|
While designing for clamping the following
factors essentially need to be considered: |
- Clamping need to be strong and rigid
enough to hold the blank firmly during machining
clamping should be easy, quick and consistently adequate
- Clamping should be such that it is
not affected by vibration, chatter or heavy pressure the
way of clamping and unclamping should not hinder loading
and unloading the blank in the jig or fixture the clamp
and clamping force must not damage or deform the
workpiece
- Clamping operation should be very
simple and quick acting when the jig or fixture is to be
used more frequently and for large volume of work
- Clamps, which move by slide or slip
or tend to do so during applying clamping forces, should
be avoided
- Clamping system should comprise of
less number of parts for ease of design, operation and
maintenance
the wearing parts should be hard or hardened and also be
easily replaceable
- Clamping force should act on heavy
parts and against supporting and locating surfaces
- Clamping force should be away from
the machining thrust forces
- Clamping method should be fool proof
and safe
- Clamping must be reliable but also
inexpensive
|
Type of clamps: |
|
Clamping faults |
Faulty clamping can lead to various
problems: |
- Workpiece can come detached from
clamp or vice and can lead to serous injury
- Vibration of machine and work
- Bending and distortion of workpiece
- Clamp damage on workpiece surface
|
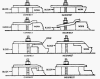 |
|
|
|