Drilling operations |
Drilling is an operation of making a circular
hole by removing a volume of metal from the job by cutting
tool called drill. A drill is a rotary end-cutting tool with
one or more cutting lips and usually one or more flutes for
the passage of chips and the admission of cutting fluid. |
Videos |
|
Types of Drilling Machine Operations: |
|
|
Centre drilling |
Centre drills
are usually double sided drills with a 60' stepped point,
held in a drill chuck or collet chuck in a lathe or
drilling machine.
The purpose of the centre drill is to create an accurate
centre hole in the face of a job so as a live centre can be
inserted to support the weight and load of the job, whilst
turning it.
Longer jobs generally require a live centre from the
tailstock of the lathe to support the job, which prevents
chatter and run out.
Centre drills can also be very useful in spotting or
starting a precise hole, which will also give a chamfer on
the hole.
Centre drills come in British Standard Sizing ( No.1 -
No.6); eg. No.3 centre drill; are also available in metric
sizes. |
|
Drilling |
Drilling is an
operation of making a circular hole by removing a volume of
metal from the job by cutting tool called drill. A drill is
a rotary end-cutting tool with one or more cutting lips and
usually one or more flutes for the passage of chips and the
admission of cutting fluid. |
(See drill bit terminology) |
|
Drill bit
material |
Drill bit
material is depended on the type of material that is been
drilled: |
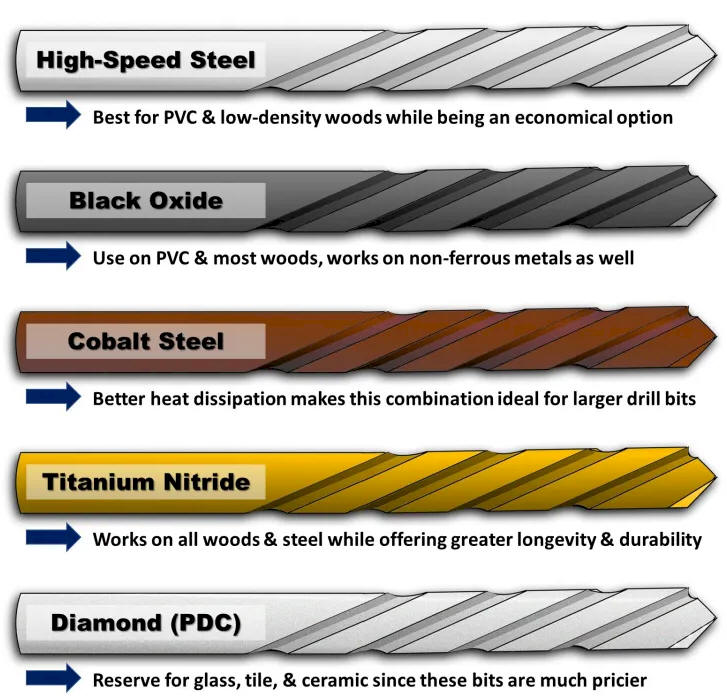
|
Masonry
drill bit (cement, tiles) |
When you buy a
drill bit for concrete, getting the right one to achieve the
best results possible is important. A formidable drill made
of a hard metal such as tungsten carbide is necessary
to drill through stone, granite, marble, or granite. Masonry
drill bits are also specifically designed for stone and can
effortlessly bore through these challenging materials.
These drill bits recommended all feature carbine tungsten as
the primary material. These bits can endure hard stone
drilling. Wide flutes on masonry drill bits enable them to
pull large amounts of material away from the bit as they
drill, preventing particles from jamming it. |

|
Drill angels |
The two most common drill bit point angles
are 118 degrees and 135 degrees. The difference between the
two is the shape; a 118-degree bit is steeper, more pointed
and has a smaller chisel.
The 118-degree bit cuts more aggressively and
is generally used for drilling into soft material like wood.
Although it can puncture through steel, if used for this,
the steeper cutting angle also will cause it to dull more
quickly.
A 135-degree bit typically is used for
drilling into harder materials, because the pitch makes it
easier to drill repeated holes into tougher material.
Drilling into thin plate material also
require a drill bit with a large included angle
It is important that cutting lips must be of
equal length to ensure holes are correct size, If
cutting lips are not equal it will lead to over sized, and a
lot of chatter during drilling. |
|
|
|
Reaming
(see
reaming detail) |
This is finishing of a drilled hole in order
to obtain the specific size, fine surface, and making the
diameter the same size form end to end. The sufficiently
smooth hole is desired and called will be called a precision
hole as greater accuracy is required. |
|
|
Tapping
(see
tapping detail) |
This drilling machine operation is by
creating tapped (threaded) hole on a workpiece. It is
achieved by producing a non-tapped hole on the material,
using a specified size drill bit. A tapping attachment will
then be used to create the threading using a standard
drilling machine.
This tapping attachment is held in the spindle of the drill
press, which is accurately centres on the drilled hole. |
|
|
|
Boring |
Boring operation is performed to enlarge the
diameter of the existing hole which means it is always
performed after drilling. |
|
|
|
Counter boring |
Counter boring is the process of using
counter bores on a drilling machine to create a hole over
the screw clearance. This newly formed hole is designed to
let the screw rest in its place and not stick out.
Creating counter bores is achieved by using the drilling
machine, which uses drill bits that have a tip. Creating
counter bores is relatively simple. However, you must know
when to stop. Otherwise, you may make a hole that’s too wide
and can’t grip the fastener properly.
A counter bore allows you to completely hide the cap screw
underneath the surface. This way, the head of the cap screw
does not interfere with the design of the product and can
help the finished product look more aesthetically pleasing. |
|
|
|
Counter sinking |
Countersinking a hole is to cut a conical
hole into a metal object. This process is normally used to
create space for the head of a screw or bolt to sit flush
with the surface of the material or to clean away burrs left
from drilling and tapping. |
|
|
|
Spot facing |
Spot facing is a machined feature in which a
certain region of the workpiece (a spot) is faced, providing
a smooth, flat, accurately located surface. This is
especially relevant on work pieces cast or forged, where the
spot face's smooth, flat, accurately located surface stands
in distinction to the surrounding surface whose roughness,
flatness, and location are subject to wider tolerances and
thus not assured with a machining level of precision.
The most common application of spot facing
is facing the area around a bolt hole where the bolt's head
will sit, which is often done by cutting a shallow counter
bore, just deep enough "to clean up" that is, only enough
material is removed to get down past any irregularity and
thus make the surface flat.
Other common applications of spot facing
involve facing a pad onto a boss, creating planar surfaces
in known locations that can orient a casting or forging into
position in the assembly; allow part marking such as
stamping or nameplate riveting; or offer machine-finish
visual appeal in spots, without the need for finishing all
over |
|
|
|